CMMS, or Computerized Maintenance Management Systems, are revolutionizing how businesses handle maintenance. Forget sticky notes and spreadsheets – CMMS software streamlines everything from scheduling preventative maintenance to tracking equipment repairs. This deep dive explores CMMS selection, implementation, data management, and future trends, showing you how to optimize your maintenance operations and boost your bottom line. We’ll cover everything from choosing the right software for your business size to leveraging predictive maintenance with IoT sensors.
This guide covers a wide range of topics, from the nitty-gritty details of software selection and implementation to the strategic benefits of using CMMS for predictive maintenance and improved data analysis. We’ll also explore the unique challenges and opportunities presented by different industries and the integration of cutting-edge technologies like IoT and mobile apps. Get ready to level-up your maintenance game!
CMMS Software Selection Criteria
Choosing the right CMMS (Computerized Maintenance Management System) software is crucial for optimizing maintenance operations and maximizing asset lifespan. The decision hinges on several factors, including business size, budget, specific needs, and desired integration capabilities. A thorough evaluation process, considering both short-term and long-term implications, is essential for a successful implementation.
CMMS Software Comparison
Selecting the right CMMS involves comparing various options. The following table presents a comparison of four leading CMMS solutions, highlighting their key features and pricing models. Note that pricing can vary greatly depending on the number of users, modules selected, and contract terms. Always request a customized quote from each vendor.
Feature | UpKeep | Fiix | Hippo CMMS | MPulse |
---|---|---|---|---|
Pricing Model | Subscription-based, tiered pricing | Subscription-based, tiered pricing | Subscription-based, tiered pricing | Subscription-based, tiered pricing; also offers on-premise solutions |
Work Order Management | Robust features, mobile accessibility | Streamlined workflow, automated notifications | Comprehensive features, customizable workflows | Advanced scheduling, resource allocation |
Preventive Maintenance | Automated scheduling, customizable checklists | Flexible scheduling options, integration with inventory | Detailed reporting and analytics, proactive alerts | Predictive maintenance capabilities, integration with IoT devices |
Inventory Management | Track parts, consumables, and equipment | Real-time inventory tracking, automated ordering | Detailed inventory control, low-stock alerts | Advanced inventory optimization, integration with procurement systems |
Reporting & Analytics | Customizable dashboards, key performance indicators (KPIs) | Data visualization tools, trend analysis | Comprehensive reporting, data export options | Advanced analytics, predictive modeling |
Mobile Accessibility | Yes, fully integrated mobile app | Yes, user-friendly mobile interface | Yes, mobile-optimized platform | Yes, robust mobile functionality |
CMMS Software Selection for Businesses of Different Sizes
The ideal CMMS solution varies significantly depending on the size and complexity of a business. Small businesses often prioritize ease of use and affordability, while larger enterprises require more advanced features, scalability, and integration capabilities.Small businesses (fewer than 50 employees) may benefit from simpler, user-friendly CMMS solutions with a focus on core maintenance functions like work order management and preventive maintenance.
They might prioritize cloud-based solutions for accessibility and cost-effectiveness. A company like a small bakery might choose UpKeep for its ease of use and mobile accessibility.Mid-sized businesses (50-250 employees) often require more sophisticated features, such as advanced reporting and analytics, inventory management, and integration with other business systems. They need a scalable solution that can grow with their business.
A regional chain of restaurants, for example, might find Fiix suitable due to its streamlined workflow and inventory integration capabilities.Large enterprises (over 250 employees) typically require highly customizable, enterprise-grade CMMS solutions with robust security features, advanced analytics, and seamless integration with existing ERP and CRM systems. They might prioritize solutions offering predictive maintenance and IoT integration. A large manufacturing plant might opt for MPulse due to its advanced scheduling and predictive maintenance capabilities.
CMMS Software Integration Capabilities
Seamless integration with other business systems is a crucial consideration when selecting CMMS software. Effective integration can significantly improve efficiency and data accuracy by eliminating data silos and automating workflows.CMMS software can integrate with various systems, including Enterprise Resource Planning (ERP) systems (e.g., SAP, Oracle), Customer Relationship Management (CRM) systems (e.g., Salesforce, HubSpot), and other business intelligence tools. Integration with ERP systems allows for streamlined data exchange regarding inventory, purchasing, and financial reporting.
Integration with CRM systems can enhance customer service by providing timely updates on maintenance requests. For example, integrating a CMMS with an ERP system can automate the process of ordering replacement parts when inventory levels fall below a predefined threshold, reducing downtime and improving efficiency. This integration allows for real-time visibility across different departments, enhancing overall operational effectiveness.
CMMS Implementation Strategies
Successfully implementing a CMMS (Computerized Maintenance Management System) is crucial for maximizing its benefits. A well-planned rollout minimizes disruption and ensures a smooth transition to the new system, leading to improved maintenance efficiency and reduced downtime. This section Artikels strategies for a phased implementation and best practices for user training and change management.
Phased Implementation Plan for a Medium-Sized Manufacturing Company
A phased approach is recommended for medium-sized manufacturing companies adopting a new CMMS. This minimizes risk and allows for adjustments based on early feedback. The following plan Artikels four phases:
- Phase 1: Planning and Preparation (2-4 weeks): This involves selecting the CMMS software, defining project scope and goals, assembling a project team, and establishing communication protocols. Key tasks include data migration planning (from existing systems, if any), user identification and roles assignment, and defining key performance indicators (KPIs) for measuring success.
- Phase 2: System Configuration and Data Migration (4-6 weeks): This phase focuses on configuring the CMMS software to meet the company’s specific needs, including customizing workflows, setting up user accounts, and importing existing asset and maintenance data. Data cleansing and validation are critical steps to ensure data accuracy.
- Phase 3: User Training and Testing (2-4 weeks): Comprehensive user training is essential. This phase includes hands-on training sessions for all users, focusing on practical application of the system. Pilot testing with a small group of users allows for identifying and resolving any issues before full deployment. This phase also incorporates feedback loops to refine the system configuration and training materials.
- Phase 4: Go-Live and Post-Implementation Support (Ongoing): This involves a phased rollout of the CMMS across different departments or work areas. Continuous monitoring of KPIs, user support, and system maintenance are crucial for long-term success. Regular system reviews and updates should be scheduled to ensure optimal performance and address evolving needs.
Best Practices for User Training and Change Management
Effective user training and change management are paramount for a successful CMMS implementation. Resistance to change is common, so a proactive approach is needed.
- Develop a comprehensive training program: This should include both classroom-style training and hands-on practice with the system. Tailor training to different user roles and levels of technical expertise.
- Engage users early and often: Involve users in the selection and implementation process. Their input is invaluable for ensuring the system meets their needs and for gaining buy-in.
- Provide ongoing support: Establish a help desk or support system to address user questions and issues after go-live. Regular updates and communication keep users informed about system enhancements and best practices.
- Incentivize adoption: Reward users for actively using the system and providing feedback. This can help to build positive attitudes towards the new system.
- Measure and track success: Monitor KPIs to assess the effectiveness of the CMMS implementation and identify areas for improvement. Regular reporting and feedback sessions keep the project on track.
CMMS Go-Live Checklist
A thorough checklist ensures a smooth transition to the new system.
- Data migration complete and validated: All relevant data has been successfully migrated and verified for accuracy.
- User training completed: All users have received appropriate training and are comfortable using the system.
- System testing completed successfully: All system functionalities have been tested and any issues resolved.
- Communication plan in place: A clear communication plan is in place to keep users informed throughout the go-live process.
- Support team ready: A dedicated support team is available to address user questions and issues.
- Backup and recovery plan in place: A robust backup and recovery plan is in place to prevent data loss.
- Post-implementation review scheduled: A post-implementation review is scheduled to assess the success of the project and identify areas for improvement.
CMMS Data Management and Reporting
Accurate and reliable data is the lifeblood of any effective CMMS. Without it, your system becomes a glorified to-do list, failing to deliver the insights needed for proactive maintenance and cost savings. This section explores the crucial role of data management and the powerful reporting capabilities that unlock the true potential of your CMMS.Data integrity is paramount. Inaccurate data entry leads to flawed analysis, poor decision-making, and ultimately, wasted resources.
Implementing robust data validation procedures, such as automated checks and user training, is essential to ensure the accuracy and reliability of your CMMS data. This includes verifying data types, ranges, and consistency across different data fields. For example, ensuring that work order completion dates are chronologically consistent with start dates, or that equipment IDs are unique and correctly linked to their respective asset records, are crucial steps in maintaining data quality.
Data Validation Techniques
Effective data validation goes beyond simply checking for missing fields. It involves implementing a multi-layered approach. This includes establishing standardized naming conventions for assets and parts, using dropdown menus for pre-defined options to minimize typographical errors, and employing automated data checks to identify inconsistencies and flag potential problems for review. Regular data audits should also be conducted to identify and correct any inaccuracies that might have slipped through the initial validation process.
These audits can help refine validation rules and processes over time, improving data quality continuously.
Insightful CMMS Reports for Improved Maintenance Efficiency
CMMS data provides a wealth of information that can be leveraged to significantly improve maintenance efficiency. Well-designed reports can highlight areas for improvement, predict potential failures, and optimize resource allocation. For example, reports showing the frequency and duration of equipment downtime can identify critical assets requiring more preventative maintenance. Similarly, reports on maintenance costs per asset or per work order can pinpoint areas where cost optimization strategies might be implemented.
Analyzing historical data on repair times can help optimize scheduling and resource allocation for future maintenance tasks.
Sample Maintenance KPI Report
The following report illustrates key performance indicators (KPIs) related to maintenance costs and equipment uptime. This type of report provides a concise overview of the maintenance performance, facilitating informed decision-making.
KPI | Value | Target | Status |
---|---|---|---|
Mean Time Between Failures (MTBF) | 120 days | 150 days | Below Target |
Mean Time To Repair (MTTR) | 2 days | 1.5 days | Above Target |
Maintenance Cost per Asset (Annual) | $5,000 | $4,500 | Above Target |
Preventive Maintenance Compliance Rate | 95% | 98% | Below Target |
Equipment Uptime | 98% | 99% | Below Target |
CMMS and Predictive Maintenance
Predictive maintenance, a proactive approach to maintenance management, leverages data analysis to anticipate equipment failures before they occur. A robust CMMS (Computerized Maintenance Management System) is crucial in facilitating this strategy, providing the platform to collect, analyze, and act upon the data that informs predictive maintenance decisions. Without a CMMS, the data collection and analysis required for effective predictive maintenance would be significantly more difficult and less efficient.Predictive maintenance, powered by a CMMS, moves beyond reactive and even preventative maintenance, allowing organizations to optimize maintenance schedules and resource allocation, ultimately minimizing downtime and maximizing operational efficiency.
This proactive approach leads to significant cost savings in the long run by preventing catastrophic failures and reducing the need for emergency repairs.
Sensor Data Integration for Predictive Maintenance
The effectiveness of predictive maintenance hinges on the ability to collect and interpret relevant data from various sources. A CMMS serves as the central hub for integrating data from diverse sensors deployed across equipment. This integrated data provides a holistic view of equipment health, enabling more accurate predictions of potential failures.The types of sensor data commonly integrated include vibration data (measuring imbalances and wear), temperature data (indicating overheating or cooling system issues), pressure data (revealing leaks or blockages), current and voltage data (detecting electrical anomalies), and acoustic emission data (capturing subtle changes indicative of wear).
For example, a manufacturing plant might integrate vibration sensors on its critical machinery. The data collected by these sensors, which measures vibration frequency and amplitude, would then be fed into the CMMS. Anomalies in the vibration data could signal impending bearing failure, allowing for timely intervention before the failure causes a costly production shutdown. Similarly, temperature sensors on a motor might reveal an overheating trend before the motor burns out.
Reduced Downtime and Maintenance Costs through Predictive Maintenance
By leveraging the data collected and analyzed through the CMMS, predictive maintenance significantly reduces both downtime and maintenance costs. Predictive maintenance allows for scheduled repairs during periods of low production or planned downtime, minimizing disruption to operations. Furthermore, it prevents catastrophic failures that can lead to extensive downtime and expensive emergency repairs.For instance, a company using predictive maintenance based on sensor data from a CMMS might identify a potential pump failure a week before it occurs.
This allows them to schedule the pump’s replacement during a planned maintenance window, preventing a production line shutdown. The cost of replacing the pump during scheduled maintenance is significantly lower than the cost of an emergency repair, which would also involve lost production time. Moreover, this proactive approach extends the lifespan of equipment, reducing the overall frequency of replacements and associated costs.
In essence, predictive maintenance using a CMMS transforms reactive maintenance into a proactive, data-driven strategy, resulting in a more efficient and cost-effective maintenance program.
CMMS for Different Industries

CMMS systems, while offering a core set of functionalities, need to be tailored to the specific needs and challenges of different industries. Factors like regulatory compliance, asset complexity, and the geographic distribution of operations heavily influence the selection and implementation of a CMMS. This section will explore these differences across several key sectors.
CMMS Requirements in Healthcare and Manufacturing
Healthcare and manufacturing represent two vastly different operational environments, demanding distinct CMMS functionalities. In healthcare, the focus is on ensuring patient safety and regulatory compliance (e.g., HIPAA, Joint Commission standards). This translates to a need for robust tracking of medical equipment maintenance, meticulous record-keeping, and integration with other healthcare systems. Downtime is costly, impacting patient care, so preventative maintenance scheduling and rapid response to equipment failures are paramount.
Manufacturing, conversely, prioritizes production uptime and efficiency. CMMS in this sector focuses on optimizing maintenance schedules for complex machinery, managing inventory of spare parts, and tracking production metrics linked to equipment performance. While both sectors value preventative maintenance, the specific equipment and the consequences of failure differ significantly, shaping the CMMS requirements. For example, a malfunctioning MRI machine in a hospital has vastly different consequences than a malfunctioning conveyor belt in a factory.
CMMS in Food Processing for Regulatory Compliance
The food processing industry faces stringent regulatory requirements concerning hygiene, safety, and traceability. A CMMS plays a crucial role in ensuring compliance with regulations like the FDA’s Food Safety Modernization Act (FSMA). CMMS helps track sanitation schedules for equipment, manage preventative maintenance of processing machinery, and maintain detailed records of all maintenance activities. This detailed documentation is vital for audits and demonstrating compliance.
For instance, a CMMS can track the cleaning and sanitization of a food processing line, recording the date, time, and personnel involved, ensuring traceability in case of a contamination incident. Furthermore, a CMMS can be used to manage the calibration and maintenance of critical equipment used in quality control, such as scales and thermometers. This comprehensive record-keeping significantly reduces the risk of non-compliance and potential penalties.
CMMS Implementation in Geographically Dispersed Organizations
Implementing a CMMS across multiple geographically dispersed locations presents unique challenges. Key considerations include ensuring consistent data entry and reporting across all sites, managing different time zones and local regulations, and providing adequate training and support to personnel at each location. Solutions involve selecting a cloud-based CMMS for centralized data management and accessibility, establishing clear communication channels between sites, and implementing standardized maintenance procedures and reporting templates.
The use of mobile CMMS applications can empower technicians in remote locations to easily update work orders, record maintenance activities, and access relevant information. Regular training and consistent communication are vital to maintain user adoption and ensure the CMMS effectively supports the organization’s maintenance needs across all locations. A well-implemented CMMS can overcome the challenges of geographical dispersion by creating a unified and efficient maintenance management system across the entire organization.
CMMS Security and Compliance
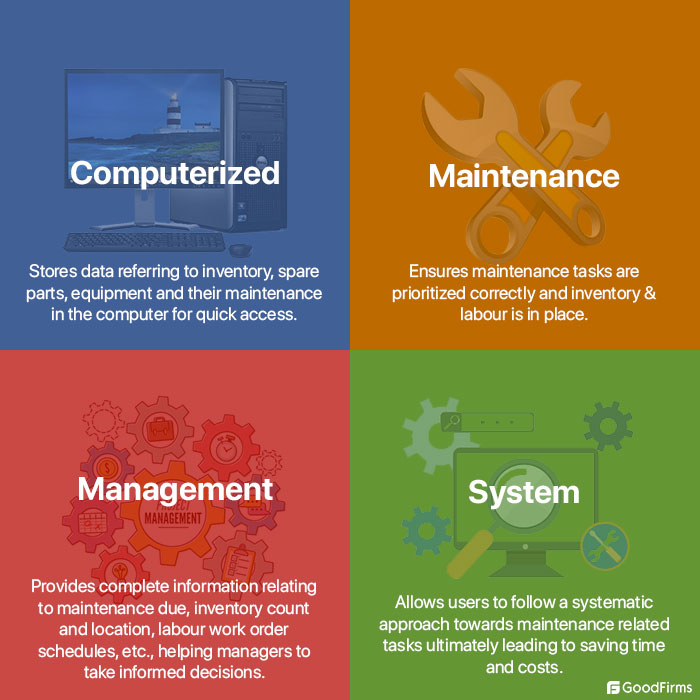
Implementing a robust CMMS system requires more than just efficient maintenance scheduling; it necessitates a comprehensive security and compliance strategy to protect sensitive data and ensure regulatory adherence. A well-structured security policy is crucial for maintaining data integrity, safeguarding business operations, and preventing costly breaches. Ignoring these aspects can lead to significant financial and reputational damage.A strong CMMS security policy encompasses various elements, all working together to protect your data and systems.
These include access control, user authentication, data encryption, regular backups, and disaster recovery planning. Compliance with relevant industry regulations is also a critical component.
Data Access Control and User Authentication
A multi-layered approach to data access control is essential. This begins with strong password policies that mandate complexity and regular changes. Role-based access control (RBAC) should be implemented, assigning permissions based on job responsibilities. For example, a technician might only have access to work orders and equipment details, while a manager might have access to reports and system-wide configurations.
This granular control prevents unauthorized access to sensitive information. Two-factor authentication (2FA) adds an extra layer of security, requiring users to provide a second form of verification, such as a code from a mobile app, in addition to their password. Regular audits of user permissions are necessary to ensure that access remains appropriate and no unnecessary privileges exist.
This prevents insider threats and ensures compliance.
CMMS System Backups and Disaster Recovery Planning
Regular backups are critical for data protection. A comprehensive backup strategy includes both on-site and off-site backups, using different storage mediums to mitigate the risk of data loss from fire, theft, or natural disasters. The frequency of backups should be determined based on the criticality of the data and the rate of change. For instance, daily backups might be necessary for high-volume transactional data, while weekly backups may suffice for less frequently updated information.
A well-defined disaster recovery plan Artikels procedures for restoring the CMMS system in case of a failure or catastrophic event. This plan should include steps for restoring data from backups, identifying alternative computing resources, and communicating with stakeholders. Regular testing of the disaster recovery plan ensures its effectiveness and identifies any weaknesses. For example, a company could simulate a server failure to test their backup and restoration procedures.
Industry Regulations and Compliance Requirements
Compliance with relevant industry regulations is crucial for CMMS data management. The specific regulations will depend on the industry and geographic location. For example, healthcare organizations must comply with HIPAA (Health Insurance Portability and Accountability Act) regulations, which dictate how protected health information (PHI) must be handled. Similarly, organizations in the financial sector may be subject to regulations like SOX (Sarbanes-Oxley Act), which mandates strict internal controls over financial reporting.
Industries handling personal data must comply with GDPR (General Data Protection Regulation) if operating in the European Union or other regions with similar data privacy laws. Understanding and adhering to these regulations is vital for avoiding penalties and maintaining public trust. Regular audits and security assessments can help organizations ensure ongoing compliance.
CMMS ROI and Cost Justification
Implementing a CMMS (Computerized Maintenance Management System) can seem like a significant upfront investment, but the long-term benefits often far outweigh the initial costs. A well-planned CMMS implementation can lead to substantial cost savings and increased efficiency, making a strong case for its financial viability. This section will explore how to calculate the ROI of a CMMS and demonstrate the potential cost savings through real-world examples.
Calculating CMMS ROI
Calculating the ROI of a CMMS involves comparing the total costs of implementation and operation against the total benefits realized. A simple formula to use is:
ROI = (Total Benefits – Total Costs) / Total Costs
. Total costs include software licensing, implementation fees, training, and ongoing maintenance. Total benefits include reduced downtime, lower maintenance costs, improved inventory management, and increased equipment lifespan. It’s crucial to quantify these benefits as accurately as possible using data from your existing maintenance operations. For example, if your current downtime costs $10,000 per hour and a CMMS reduces downtime by 10 hours per year, the annual benefit from reduced downtime alone would be $100,000.
Examples of CMMS Cost Savings
Several key areas contribute to significant cost savings with a CMMS. Improved preventative maintenance scheduling, for instance, can drastically reduce unexpected equipment failures and associated repair costs. Imagine a scenario where a critical piece of machinery fails unexpectedly, leading to a production halt costing $50,000 in lost production and overtime pay. A CMMS could have prevented this by proactively scheduling preventative maintenance, thus avoiding the costly failure.
Furthermore, optimized inventory management through a CMMS prevents overstocking of spare parts, reducing storage costs and minimizing the risk of parts obsolescence. A reduction in paperwork and manual processes, facilitated by the CMMS, also leads to labor cost savings. Finally, improved data analysis provided by the CMMS enables better decision-making, further optimizing maintenance strategies and resource allocation.
So, CMMS, right? It’s all about managing your maintenance, keeping track of everything. But what about the tax side of things? You can easily manage your tax paperwork with the help of turbotax free , which can help you stay organized. Then, once you’ve got your taxes sorted, you can get back to focusing on optimizing your CMMS system and ensuring everything runs smoothly.
Cost-Benefit Analysis Table
The following table illustrates a simplified cost-benefit analysis for a hypothetical company implementing a CMMS. Note that these figures are for illustrative purposes and should be tailored to your specific circumstances.
Category | Costs | Benefits | |
---|---|---|---|
Software Licensing | $5,000 | Reduced Downtime (10 hours/year @ $10,000/hour) | $100,000 |
Implementation | $10,000 | Reduced Repair Costs (20% reduction on $50,000 annual repairs) | $10,000 |
Training | $2,000 | Improved Inventory Management (15% reduction on $20,000 annual inventory costs) | $3,000 |
Annual Maintenance | $1,000 | Increased Equipment Lifespan (Extending lifespan by 1 year, saving $25,000 in replacement costs) | $25,000 |
Total Costs | $18,000 | Total Benefits | $138,000 |
CMMS and the Internet of Things (IoT)
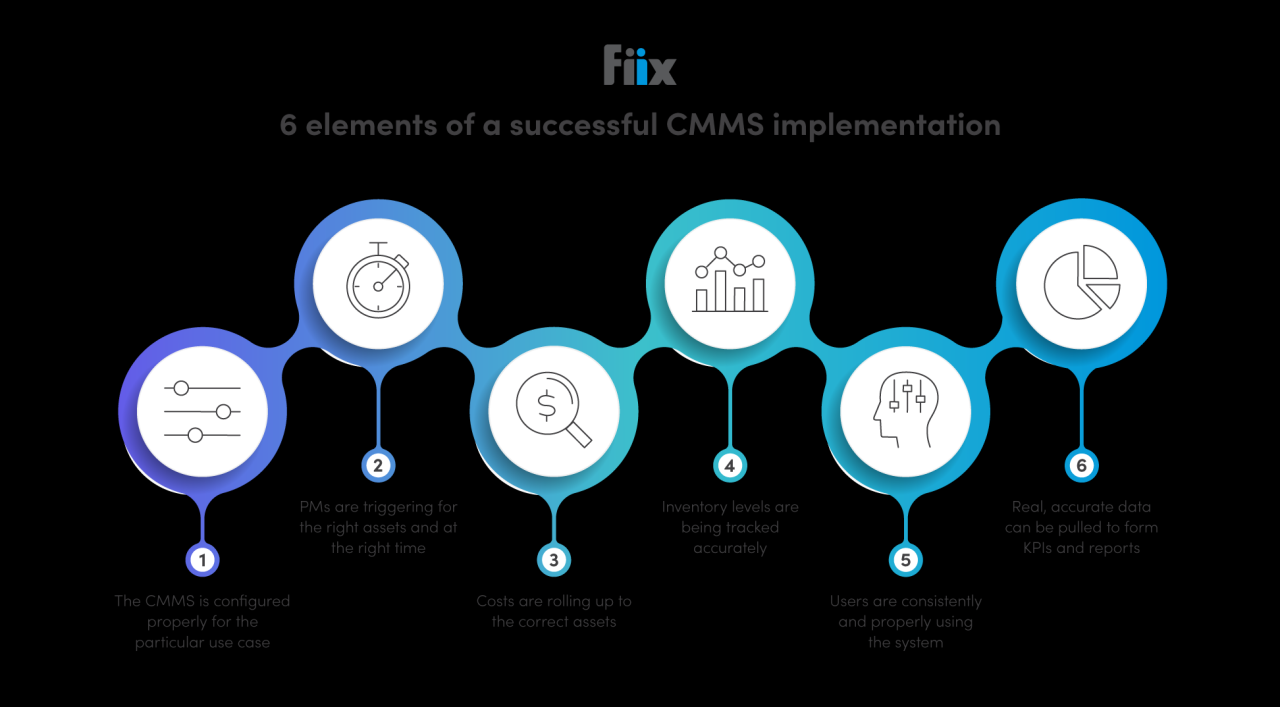
The convergence of Computerized Maintenance Management Systems (CMMS) and the Internet of Things (IoT) is revolutionizing how businesses manage and maintain their assets. By integrating smart sensors and devices into existing CMMS platforms, organizations gain access to real-time data, leading to significant improvements in efficiency, cost savings, and overall asset lifespan. This integration allows for a proactive, data-driven approach to maintenance, moving away from reactive, time-consuming methods.IoT devices provide a continuous stream of data on asset performance, environmental conditions, and operational parameters.
This data, when effectively integrated with a CMMS, transforms maintenance strategies from scheduled, preventative approaches to predictive, condition-based maintenance. This shift results in optimized resource allocation, reduced downtime, and extended equipment lifecycles. The result is a more efficient, cost-effective, and data-rich maintenance operation.
Real-time Data Enhancement of Predictive Maintenance
Real-time data from IoT sensors, such as vibration sensors, temperature sensors, and pressure sensors, provides crucial insights into the health and performance of assets. This data can be used to identify potential failures before they occur, enabling proactive maintenance interventions. For example, a vibration sensor on a pump might detect an anomaly indicating bearing wear, prompting maintenance personnel to schedule repairs before a complete failure leads to costly downtime.
This predictive approach contrasts sharply with traditional reactive maintenance, where repairs are only undertaken after a failure has already occurred. By analyzing trends and patterns in sensor data, algorithms within the CMMS can predict the remaining useful life (RUL) of an asset, allowing for optimized scheduling of maintenance activities. This minimizes disruptions and maximizes asset uptime. A large manufacturing facility, for instance, might utilize IoT sensors on its assembly line robots to predict potential motor failures, scheduling preventative maintenance during off-peak hours to minimize production interruptions.
Challenges of Integrating Diverse IoT Devices with a CMMS
Integrating diverse IoT devices from various manufacturers with a CMMS presents several challenges. The primary challenge is interoperability. Different devices use different communication protocols and data formats, requiring significant effort to standardize data acquisition and integration. Data security is another crucial consideration. The volume of data generated by IoT devices necessitates robust security measures to protect sensitive information from unauthorized access and cyber threats.
The sheer volume of data generated by a network of IoT sensors can overwhelm a CMMS if not properly managed. Efficient data processing and storage solutions are essential to prevent system overload and ensure timely analysis. Finally, the initial investment in IoT devices and the integration process can be substantial, requiring careful planning and cost justification. A company implementing IoT sensors across a large industrial plant, for instance, must carefully consider the upfront costs of hardware, software, and integration services, as well as the ongoing costs of data management and maintenance.
CMMS and Mobile Technology
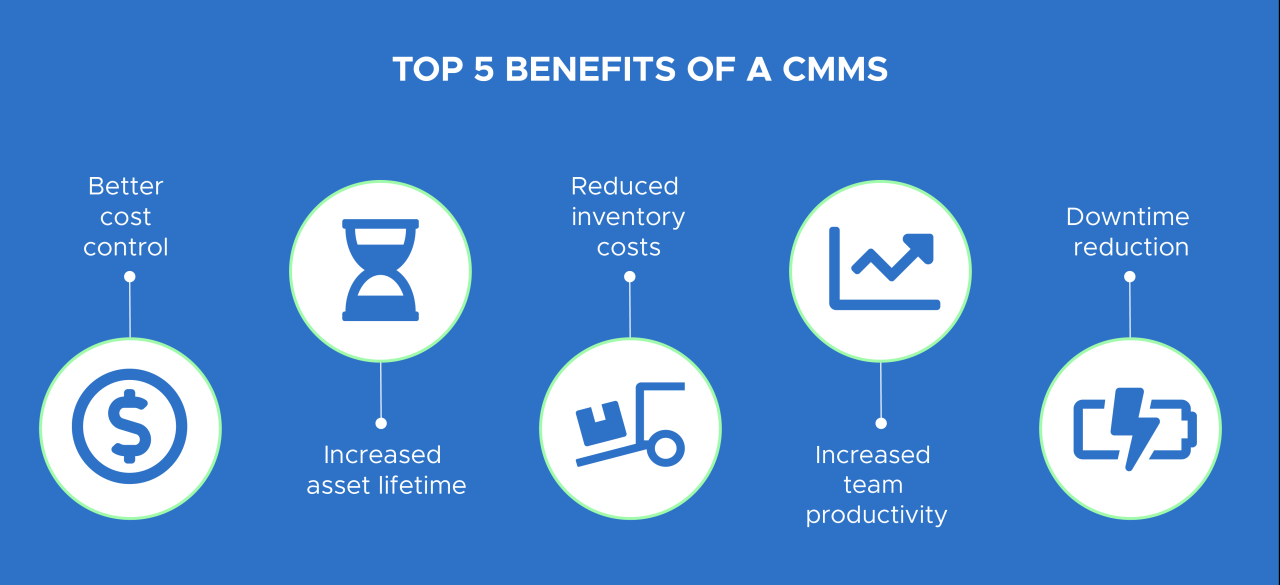
Mobile CMMS applications have revolutionized how maintenance teams operate, boosting efficiency and improving communication across the board. By putting the power of a comprehensive CMMS directly into the hands of field technicians, organizations can streamline workflows, reduce downtime, and ultimately, save money. This shift to mobile-first maintenance management is no longer a luxury, but a necessity for businesses striving for operational excellence.The advantages of integrating mobile technology into a CMMS are numerous and impactful, affecting everything from work order completion to parts inventory management.
These benefits translate directly to a more efficient, responsive, and data-driven maintenance operation.
Mobile CMMS Advantages for Field Technicians
Mobile CMMS apps empower field technicians with real-time access to crucial information, significantly improving their productivity and the overall effectiveness of maintenance operations. This eliminates the need for constant back-and-forth communication, reducing delays and improving response times to critical issues. Technicians are better equipped to handle tasks efficiently and effectively.
- Increased Efficiency: Technicians can access work orders, schematics, and maintenance history instantly, eliminating the need to return to the office or search through paper records. This translates to quicker troubleshooting and repair times.
- Improved Communication: Real-time communication features allow for seamless collaboration between technicians, supervisors, and other stakeholders. Instant updates on work order progress, material needs, and potential delays improve transparency and coordination.
- Enhanced Data Collection: Mobile apps facilitate accurate and timely data collection on completed work, parts used, and labor hours. This improves the accuracy of maintenance records and supports better decision-making.
- Reduced Paperwork: Digital work order completion eliminates the need for manual paperwork, reducing administrative overhead and minimizing the risk of lost or misplaced documents. This streamlined process frees up valuable technician time.
- Offline Functionality: Many mobile CMMS applications offer offline capabilities, ensuring technicians can continue working even in areas with limited or no internet connectivity. This is especially valuable in remote locations or during network outages.
Examples of Mobile CMMS Features Improving Work Order Management and Communication
Several key features within mobile CMMS applications directly contribute to more efficient work order management and improved communication. These features go beyond simple task listing, providing a comprehensive suite of tools to manage the entire maintenance lifecycle.
- Real-time Work Order Updates: Technicians can update work order status, add notes, and attach photos or videos directly from the field, providing supervisors with immediate visibility into progress.
- GPS Tracking and Location Services: Tracking technician location can optimize routing and dispatch, ensuring the right technician is sent to the right location quickly. This also allows supervisors to monitor technician whereabouts and provide assistance if needed.
- Integrated Inventory Management: Technicians can easily check parts availability, request replacements, and update inventory levels directly from the mobile app, reducing downtime caused by missing parts.
- Instant Messaging and Notifications: Built-in messaging systems allow for quick communication between technicians and supervisors, facilitating real-time problem-solving and coordination.
- Digital Signatures and Approvals: Mobile apps can capture digital signatures for work order completion and approvals, eliminating the need for paper-based sign-offs and speeding up the process.
Mobile CMMS Work Order Workflow
A typical workflow using a mobile CMMS app to complete a work order would follow these steps. This streamlined process enhances efficiency and accountability at each stage of the work order lifecycle.
- Work Order Creation: A work order is initiated, either by a technician, supervisor, or automatically through predictive maintenance alerts. The work order includes details such as description, priority, assigned technician, and due date.
- Work Order Assignment: The system assigns the work order to the appropriate technician based on skills, availability, and location.
- Technician Access: The assigned technician receives a notification on their mobile device and accesses the work order details, including any relevant documentation, schematics, or previous repair history.
- On-Site Work: The technician performs the necessary maintenance or repairs, utilizing the app to track time spent, parts used, and any additional notes or observations.
- Work Order Updates: Throughout the process, the technician updates the work order status and provides real-time updates to supervisors. Photos and videos can be added as needed.
- Parts Request (if needed): If parts are required, the technician can request them through the app, triggering a notification to the inventory manager.
- Work Order Completion: Once the work is complete, the technician marks the work order as finished, providing a summary of the work performed, parts used, and labor hours.
- Approval and Closure: The supervisor reviews the completed work order and approves it, officially closing the work order in the system.
Future Trends in CMMS
The CMMS landscape is rapidly evolving, driven by advancements in technology and the increasing need for efficient and data-driven maintenance strategies. We’re seeing a shift towards more intelligent, connected, and proactive systems that go beyond basic work order management. This evolution promises significant improvements in asset performance, operational efficiency, and overall cost savings.The integration of artificial intelligence (AI) and machine learning (ML) is fundamentally reshaping CMMS capabilities.
This is leading to a more predictive and proactive approach to maintenance, reducing downtime and extending the lifespan of assets.
AI and Machine Learning in CMMS
AI and ML algorithms are being incorporated into CMMS platforms to analyze historical maintenance data, identify patterns, and predict potential equipment failures. For instance, a system might analyze vibration sensor data from a pump to predict when it’s likely to fail, allowing for scheduled maintenance before a catastrophic breakdown occurs. This proactive approach minimizes unplanned downtime, a significant cost driver for many businesses.
This predictive capability allows maintenance teams to shift from reactive, emergency repairs to a more proactive, preventative maintenance strategy. The resulting reduction in unexpected failures leads to improved operational efficiency and significant cost savings. Furthermore, the ability to accurately predict maintenance needs allows for better resource allocation and optimized scheduling.
Cloud-Based CMMS Solutions
Cloud-based CMMS solutions are gaining significant traction due to their accessibility, scalability, and cost-effectiveness. Unlike on-premise systems, cloud-based CMMS eliminates the need for expensive hardware and IT infrastructure. Data is stored securely in the cloud, accessible from anywhere with an internet connection. This accessibility improves collaboration among maintenance teams, regardless of their location. For example, a field technician can access real-time information about an asset and update work orders directly from their mobile device, ensuring seamless communication and efficient workflows.
The scalability of cloud-based CMMS allows businesses to easily adapt to changing needs, adding users and features as required. This flexibility is particularly beneficial for growing companies or those experiencing seasonal fluctuations in maintenance demands.
The Future of CMMS and Digital Transformation
The future of CMMS is inextricably linked to the broader digital transformation of maintenance management. We anticipate a continued convergence of CMMS with other technologies like IoT (Internet of Things), AR (Augmented Reality), and VR (Virtual Reality). This integration will lead to even more intelligent and automated maintenance processes. For example, IoT sensors embedded in equipment will provide real-time data to the CMMS, enabling predictive maintenance and remote monitoring.
AR/VR technologies can enhance technician training and provide real-time guidance during repairs, improving efficiency and reducing errors. Imagine technicians wearing AR glasses that overlay digital instructions onto the physical equipment they are repairing. This kind of integration represents a significant leap forward in maintenance efficiency and safety. The overall impact will be a more connected, data-driven, and proactive approach to maintenance, leading to significant improvements in asset performance, reduced costs, and enhanced operational efficiency.
Companies who embrace these advancements will be better positioned to compete in a rapidly evolving market.
Closing Notes
Ultimately, implementing a CMMS is about more than just software; it’s about transforming your maintenance strategy. By carefully selecting the right system, implementing it effectively, and leveraging its data-driven insights, businesses can significantly reduce downtime, optimize maintenance costs, and improve overall operational efficiency. From preventative maintenance scheduling to predictive analytics, CMMS empowers organizations to move beyond reactive maintenance and embrace a proactive, data-driven approach to asset management.
So, ditch the outdated methods and embrace the future of maintenance management – your bottom line will thank you!
FAQ Summary
What’s the difference between CMMS and EAM?
While often used interchangeably, Enterprise Asset Management (EAM) is a broader term encompassing CMMS. EAM includes CMMS functionalities but also integrates asset lifecycle management, financial accounting, and other enterprise-wide aspects.
How much does CMMS software typically cost?
Pricing varies greatly depending on features, the number of users, and vendor. Expect to pay anywhere from a few hundred dollars per month for basic cloud-based solutions to tens of thousands for enterprise-level systems with extensive customization.
Is CMMS software difficult to learn?
Most modern CMMS platforms are designed with user-friendliness in mind. However, the learning curve will depend on the complexity of the software and the level of prior experience with similar systems. Comprehensive training is usually provided by vendors.
Can CMMS integrate with my existing ERP system?
Many CMMS solutions offer integration capabilities with popular ERP systems. Check with your vendor to ensure compatibility with your specific ERP software. Seamless integration allows for efficient data exchange between systems.
What are the key performance indicators (KPIs) I should track with a CMMS?
Key KPIs include equipment uptime, mean time to repair (MTTR), maintenance costs per unit, and preventative maintenance completion rates. Tracking these metrics helps measure the effectiveness of your maintenance strategy.